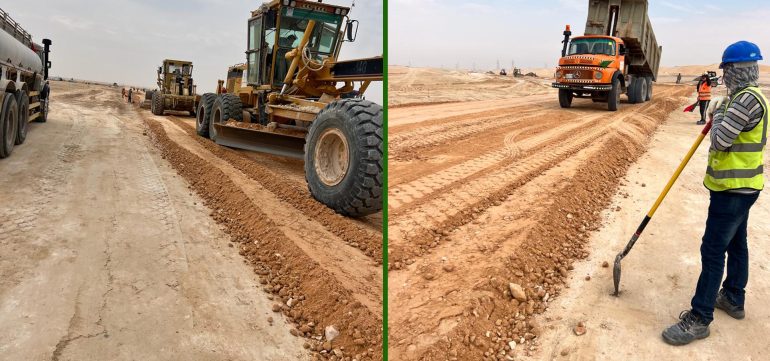
Backfilling Works
Backfilling is the process of reusing or replacing the soil that is removed during the excavation of foundations, ground bearing slabs or other groundworks to support and strengthen a structure. It protects foundations and forms part of the substructure of slabs, roadways, walkways and other groundwork elements.
Backfill can be made up of the same soil that was removed during excavation, or can be a mixture of imported soil, rocks and stones depending on the structural requirements. The need for backfilling will be established during ground investigations which will also be used by the engineers to formulate a design. Backfill is quantified in m3.
Backfill with excavated material
During the excavation process, excavated soil is set aside for later use. Once foundations or other concrete works are complete the previously set aside soil is used to backfill the foundation or other structural areas. Excess soil might be taken away from site or set aside for use in other parts of the project at a later stage. When excavated material is set aside for later use it should be protected from the elements. Excavated material should be stockpiled according to class or type of material.
The site parameters, soil type and design will dictate whether backfill with excavated materials is possible. For example, some sites might be so confined that stockpiling is not be a viable option.
Backfill with imported soil
The structural requirements for each project and situation will be unique and it might be necessary to use strengthened material for backfilling. The site constraints might also be a factor in the requirement to use imported soil.
Grading backfill
Backfill materials can generally be graded as:
Coarse grained soils – gravelly and sandy soils ranging from clay to gravel.
Fine grained soils of low to medium plasticity – inorganic clays of low to medium plasticity, inorganic silts and very fine sands of low plasticity.
Rock – suitability depending on hardness and gradation. Hard rock might be specified for crushing.
Shale – rock like material that breaks down under compaction.
Marginal materials – including fine-grained soils of high plasticity and expansive clays.
Commercial by-products – furnace slag or fly ash.
Backfill material should be homogeneous, consistent with required characteristics and free of organic matter and pockets. An engineer should visit the site to ensure that only the suitable backfill material is used.
Method for backfilling
Each project will have a unique specified method for backfilling. This will be established by the engineers of the project and described in the relevant specifications and drawings. There will be different methodologies for each element of groundworks in the project; the backfill requirements for supporting ground bearing slabs will be different to the backfill requirements for trenches.
In general, backfilling will be done in layers after the excavated areas are compacted and cleared of debris. Elements of working in confined spaces should be taken into consideration during the planning process to establish the methodology of backfilling required.